Proper Bolt Torque in Tractor Wheel Weight Mounting.
Bolt Torque for Tractor Wheel Weights. No week passes here without an inquiry from someone installing wheel weights (who has sourced their mounting hardware either from a jar in the garage, or from a local store) and they want to know how much to torque the bolts when mounting their new wheel weight. Our answer is always the same. “We don’t know.”
Proper torque depends on the specifications of the hardware and how accurate those specifications are to the bolt in your hand. Proper Torque also depends on a variety of real-world factors and can vary between applications and even between individual bolts. Temperature, the presence and type of plating on the bolt, lubrication, friction, the pitch or angle of the threads, corrosion, wear, and more all play a part.
Preload is the tension created in a fastener when it is tightened. When the tension reaches the optimal preload, the working load placed on the bolt will be distributed into the installation materials so the bolt does not have to carry the full load.
As a bolt is tightened, tension develops between the bolt head and the top of the nut and causes the bolt to stretch a small amount, much like a spring. As does a spring, the bolt constantly tries to relieve the tension and return to its relaxed state. This spring like action results in compression (clamp force) which pulls the bolt head and nut towards each other thus holding (clamping) the joint together. For the joint to be secure, a certain amount of clamp force must be maintained. Too much and the bolt will break, too little and the joint will be insecure.
Most common are bolt torque specifications determined by using a simple (probably over simplified) formula.
T=KDF or T=K x D x F
T= Torque
K = Friction Coefficient (also commonly known as the nut factor)
D= Nominal Diameter
F= Force
Note: K is usually derived from K1+K2+K3 where K1 is the geometric function of diameter and thread pitch, K2= thread friction, and K3 =function of under head friction and surface contact area. K represents (as used here) a large number of variables that have been estimated into a simple sum for use in a simple formula.
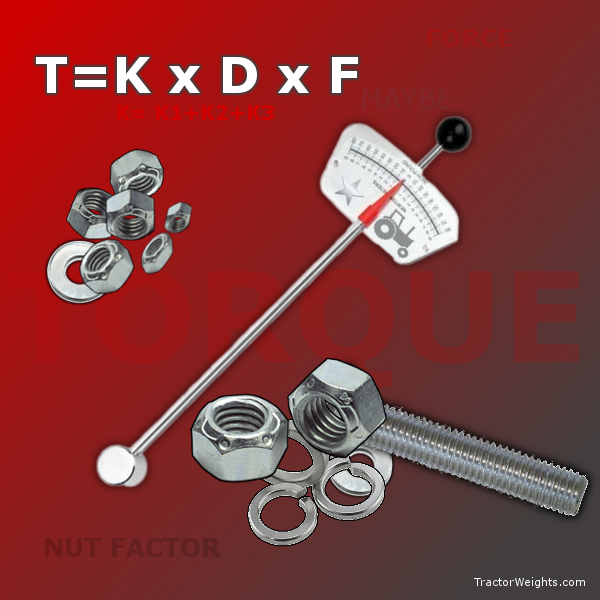
As torque is a twisting force, it only indicates work done on a joint by an installation tool and not necessarily clamping force. As torque must overcome under-head and thread friction before clamp force builds, torque is only an indirect indication of tension. Luckily, this simple formula does work pretty well for many circumstances, including the installation of wheel weights.
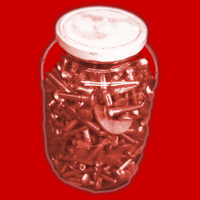
Returning now to our earlier example of the customer who sourced his bolts from a jar in the garage. We could not provide him any torque advice as we know nothing about the specifications of his hardware. We provide the recommended starting torque specifications with all of our hardware kits used for mounting wheel weights. Additionally, should you choose to source your own hardware locally, we will provide you with the complete hardware details free of charge. This would include the recommended torque specifications.
A very good reference is the Torque Tension Reference Guide published by Fastenal® and available here. Most wheel weight installations use either the standard SAE J429 Grade 5 or Grade 8 hardware or the Class 8.8 or Class 10.9 metric hardware. Some wheel weights have specific hardware requirements not discussed here, always check with your provider before purchasing hardware.
To mention one last question that we often receive: “Should I tighten the bolt or the nut?”
Either will work, but a torque value for tightening the head does not always apply to tightening the nut. They can have different “K” values (nut factor) which changes the value of the required torque. You can learn more at boltscience.com.
When installing wheel weights, it is common to have differing hole sizes between the materials as well as differing materials compromising the joint (steel wheel, cast iron wheel weight). To reduce the bearing stress on the material face and to reduce the fictional difference between materials, we always (with the exception of carriage, ribbed and flanged head bolts) recommend using flat washers on each end of your hardware.
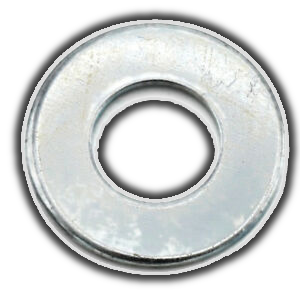
As an example of how confusing it can be: We had a service department call and inform us they were breaking some bolts and deforming others during installation. After investigation we learned; the specification they had read was in Newton-Meters and they were using a torque wrench in Foot-Pounds. They were over tightening each of the bolts by 133 foot-pounds in this instance. Make sure your tools match the specifications or ensure you have done the correct conversions.
Always remember that over tightening or under tightening of fasteners can result in equipment failure or injury. Keep in mind, that even with absolutely perfect torque, the preload can be off by as much as 20-30 percent.
Most of the torque applied is used to overcome friction with only a small percentage of the overall torque providing the clamp force. Loosening often occurs due to shock, vibration, and or dynamic loads (transversely applied alternating forces). Loosening can also occur due to settlement, creep, and or relaxation. It is imperative that checking the torque on your wheel weights should be part of your routine maintenance program as well as a (more often) inspection process.
Have Questions? We invite you to contact us.
This blog is general information only, representing the opinions of the author, and does not cover all aspects of the subject matter. Use of the information contained herein is voluntary.